Enhancing the Monofiller
Modularity, Speed & HMI for Scaldopack
Long story short
Scaldopack, a Belgium-based manufacturer of spouted package filling machines, sought to modernize its line-up to improve efficiency and adaptability. CTRL Engineering developed a modular, scalable software solution to boost production speed, enhance flexibility, and improve user experience. By eliminating dead time, synchronizing movements, and reducing reliance on physical sensors, we achieved higher throughput. Our solution prioritized error handling and ease of use to ensure smooth operation. A custom Beckhoff HMI streamlined operator interaction with role-based access. The result is a future-proof automation system maximizing reliability, adaptability, and efficiency.
The Challenge: Modernizing Software for Flexibility & Robustness
Scaldopack’s machines required a complete software redesign to support modular configurations for various setups, ensure seamless sequencing, and maintain high production output without sacrificing reliability. Additionally, the new system needed an intuitive, role-based HMI and the ability to handle real-world disruptions with minimal downtime.
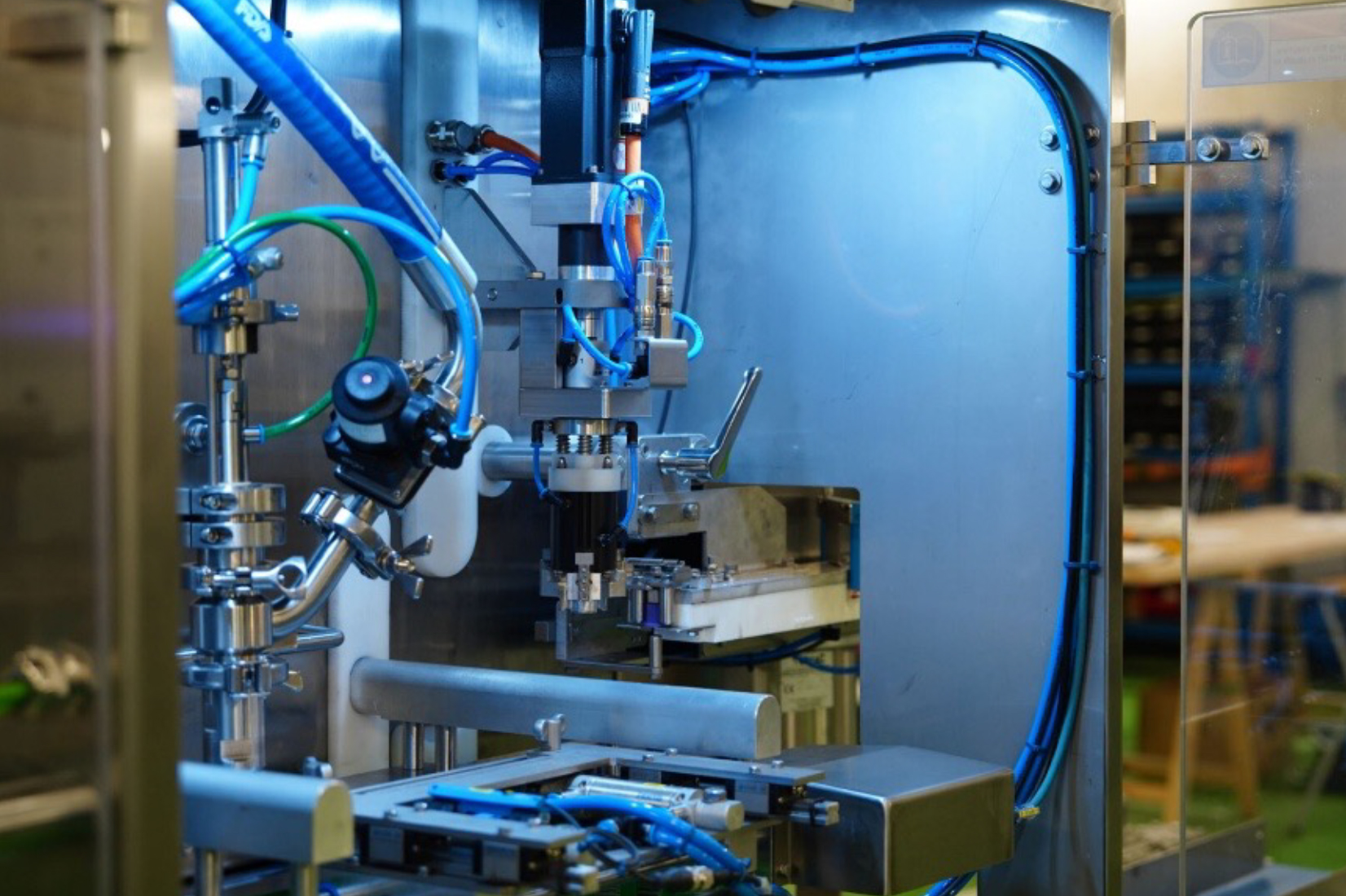
Our Approach
Optimizing Speed & Efficiency
One of the primary goals was increasing production speed. We eliminated unnecessary waiting times by optimizing sequencing and preventing delays caused by mechanical dependencies. Movements were synchronized to allow continuous operation, significantly reducing cycle times. Many redundant physical sensors were replaced with software-based tracking mechanisms, simplifying the system while improving reliability. These enhancements pushed Scaldopack machines beyond their previous speed limitations, making them faster and more efficient than ever before.
A Modular & Scalable Software Architecture
Since custom-built machines in the food and beverage industry often share similar structures but vary in components, we developed a flexible software stack rather than writing separate programs for each configuration. Whether controlling a single or multi-head filling station, the software ensures consistent and efficient operation. This modular approach allows for easy adaptation to different machine setups, making the system highly scalable.
Handling Errors & Recovery
Machines don’t always run smoothly, so we designed the software to detect, manage, and recover from unexpected issues without causing unnecessary downtime. Automated error detection and classification provide clear operator feedback, while emergency stop handling ensures quick resumption of operations. The system also includes intuitive fault recovery mechanisms that operators can manage without technician intervention. Diagnostic logging further enhances reliability by facilitating long-term troubleshooting and system monitoring.
A Smarter, More User-Friendly HMI
To complement the software, we developed a custom multilingual HMI using Beckhoff technology, designed with usability in mind. The interface displays only relevant information, reducing visual clutter and streamlining operations. Role-based access ensures secure system control at different levels. Operators can monitor real-time status and manage essential controls, maintenance users have access to diagnostics and motion controls, while super users can configure the full system. This structured approach improves efficiency, security, and ease of operation.
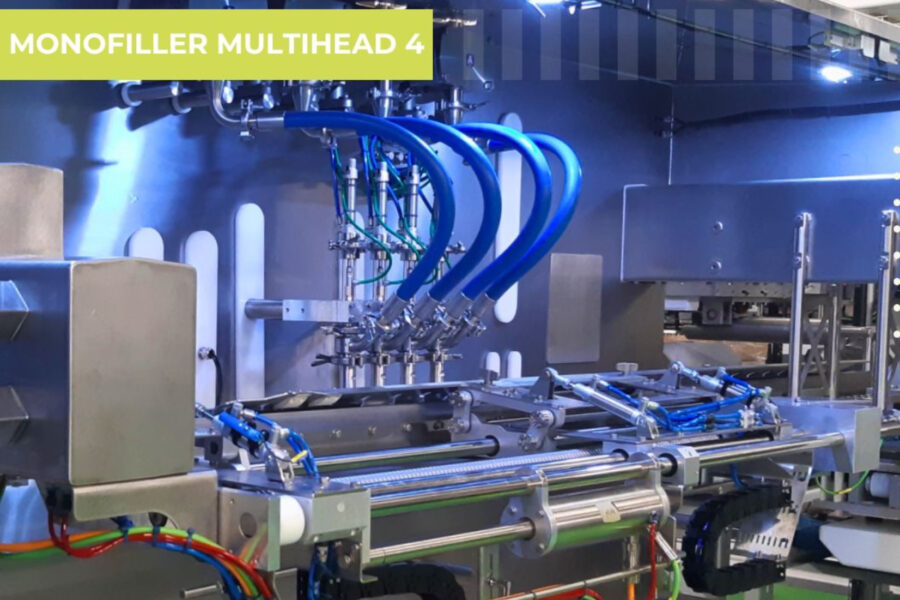
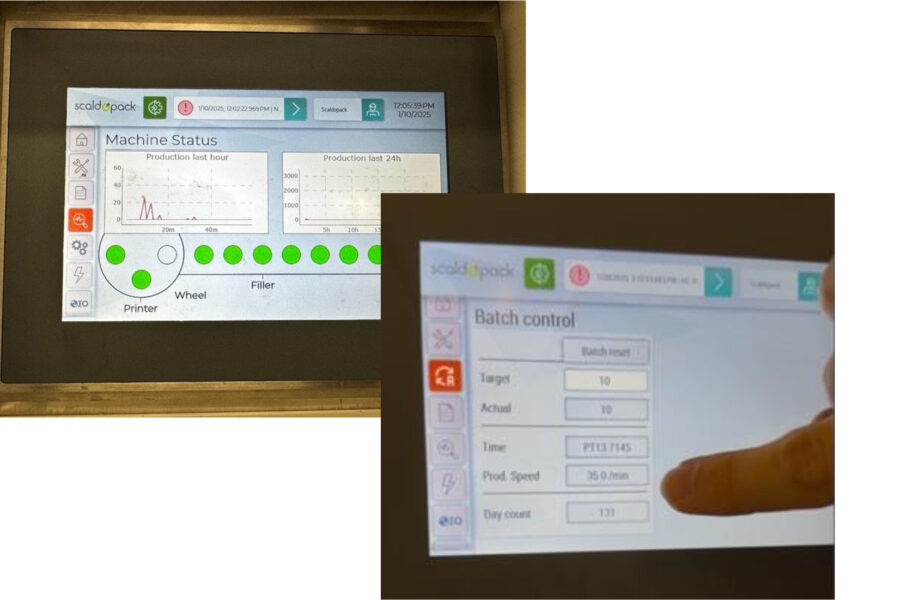
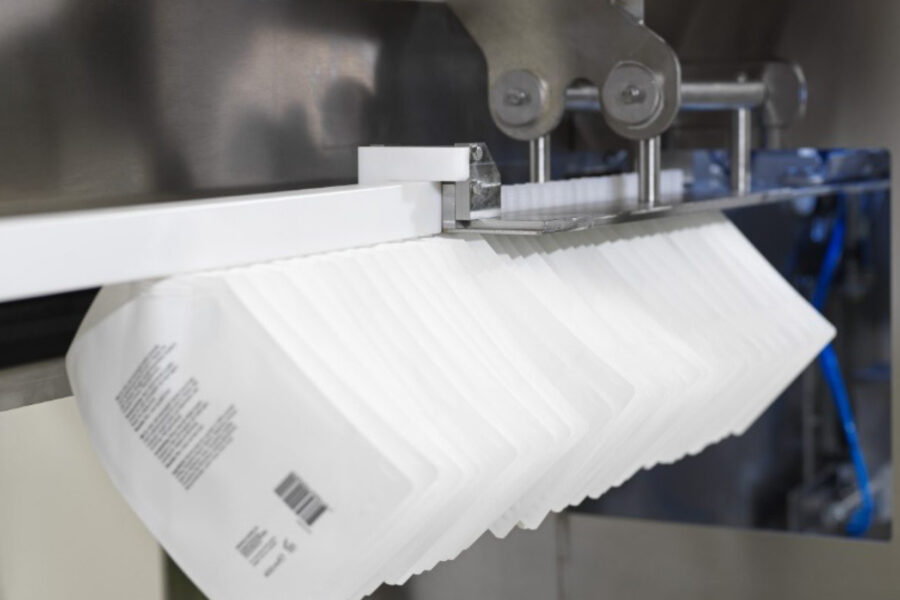
The Results: A Faster, More Adaptive & Future-Proof Solution
With these upgrades, Scaldopack machines now deliver higher production speeds, improved reliability, and greater flexibility for different machine setups. Optimized error handling minimizes downtime and reduces reliance on technicians, while the streamlined HMI makes machine control more intuitive. By implementing modular software, synchronized motion sequencing, and advanced recovery mechanisms, we have transformed Scaldopack’s equipment into high-performance automation systems ready for the future.
Why It Matters to you?
Automation is about more than just running machines—it’s about making them run faster, more reliably, and with minimal downtime. By eliminating inefficiencies, synchronizing movements, and reducing reliance on physical sensors, we have increased production speeds while keeping the system flexible and easy to maintain. Whether the goal is boosting output, simplifying operator control, or ensuring machines can handle unexpected events, robust software and intuitive HMIs are critical. Investing in scalable automation solutions future-proofs production lines and helps businesses stay ahead in a competitive industry. With CTRL Engineering’s expertise, Scaldopack’s filling machines are now equipped for long-term success in automated filling solutions.