Pumps
Lobe pump
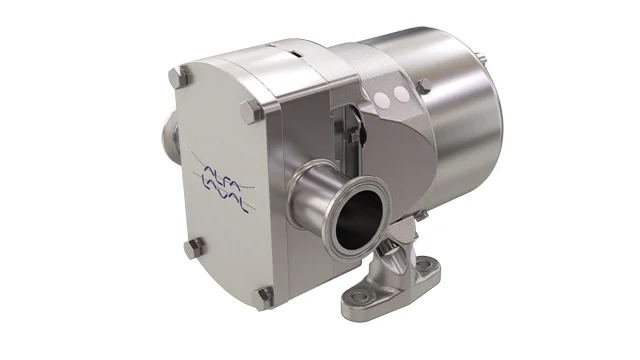
A lobe pump is a positive displacement pump that uses rotating lobes to move fluids.
Key features:
- Hygienic Design: Ideal for sanitary applications, metals seals
- Versatility: Handles very low to high-viscosity fluids and with non abrasive solid parts.
- Gentle Handling: Provides smooth, non-pulsating flow. Good for Hot fill, cold fill or refrigerated filling
Applications
- Food and Beverage: Dairy, syrups, jams, yogurt, fruit pure.
- Pharmaceuticals: Sensitive products.
- Cosmetics: Creams and lotions.
- Chemicals: Low to high viscous products and shear-sensitive fluids.
Advantages
- Continuous flow pumps: good for dosing large volume containers
- Easy to Clean: Meets strict hygiene standards, with CIP (Clean-in-Place) systems
- Efficient: Consistent flow rates.
Disadvantages
- Volumetric dosing Accuracy: Typically +/-1%.
- Cost: Higher initial investment.
Centrifugal pump
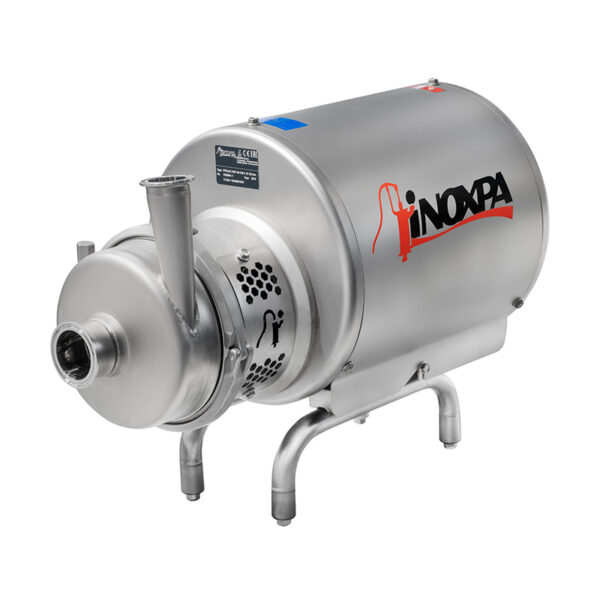
An affordable solution to move fluids by converting rotational kinetic energy to hydrodynamic energy.
Key features:
- Hygienic Design: Stainless steel for sanitary use.
- High Flow Rates: Efficient for large volumes.
- Continuous Flow: Steady, non-pulsating flow.
Applications
- Beverages: Juice, milk, soft drinks.
- Dairy: Milk, hot ghee
- Brewing: Beer and wort transfer.
- Food Ingredients: Oils, syrups, sauces.
- Technical products: low to medium viscosity up to 300 cps.
Advantages
- Continuous flow pumps: good for dosing large volume containers
- Efficient: Ideal for low to medium-viscosity fluids.
- Easy Cleaning: Compatible with closed loop cleaning CIP systems.
- Cost-Effective: Lower initial cost and easy maintenance.
Disadvantages
- High Shear: Can damage shear-sensitive products.
- Limited Viscosity Handling: Not suitable for fluids above 300cps.
- Priming Needed: May require priming.
Membrane or Diaphragm pump
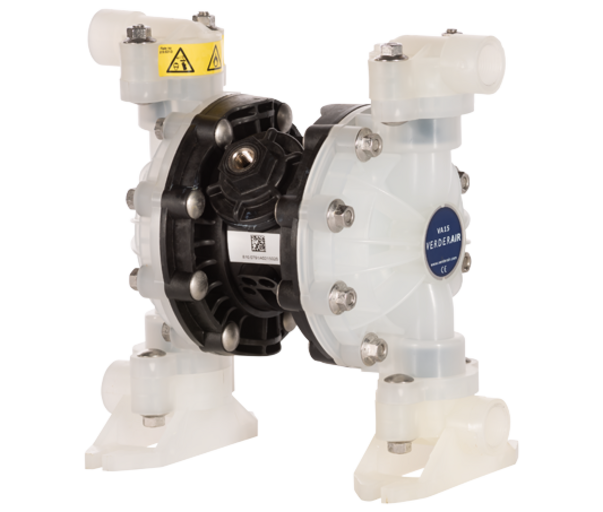
A membrane pump, or diaphragm pump, is an easy solution for transferring products, utilizing a flexible membrane to move fluids gently and precisely.
Key features:
- Gentle Handling: Ideal for shear-sensitive products.
- Self-Priming: Handles a variety of fluids, including those with solids.
- Easy Setup: Requires only compressed air.
- Easy to Clean: Compatible with CIP (Clean-in-Place) systems or simple rinsing.
Applications
- Food Processing: Sauces, syrups, and other low to high viscous products, dairy products.
- Beverages: Juice, wine, and other drinks.
- Chemicals: Low to high viscous products, can handle corrosive and abrasive fluids
Advantages
- Continuous flow pumps: good for dosing large volume containers
- Durability: Handles abrasive and corrosive fluids well.
- Versatile: Accommodates a wide range of viscosities.
- Easy setup: only one line of compressed air is required.
Disadvantages
- Noisy and compressed air consumption. Not good for clean room applications.
- Pulsating Flow: May need pulsation dampeners for smooth operation.
Piston pump
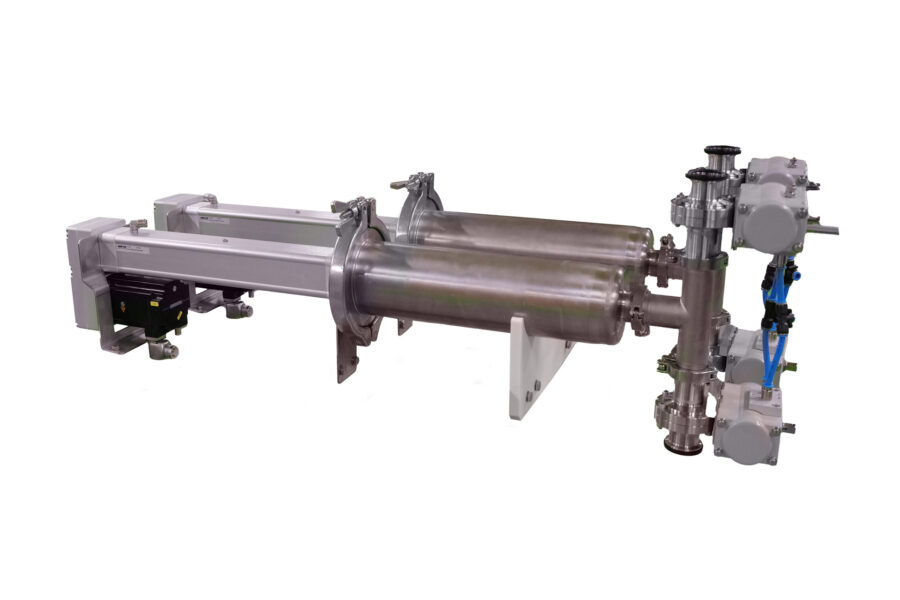
A piston pump is a type of positive displacement pump that uses a piston to move fluids, offering high precision and pressure capability.
Key features:
- Positive Displacement: Traps and displaces fluid.
- High Pressure: Effective for high-pressure applications.
- Precision: Accurate dosing and control.
- Servo-Controlled: Reliable, self-priming, and operates directly from IBCs or other product vessels.
- Manual Cleaning: Scaldopack pumps allow tool-free manual disassembly for daily cleaning and changing of seals.
Applications
- Food: Syrups, sauces, juices, milk, yogurt, broths, tea, etc.
- Pharmaceuticals: Sterile fluids.
- Chemicals: Low to high viscous products
Advantages
- High Pressure: Handles high viscous products and can generate high dosing pressures.
- Precise Control: Accurate dosing.
- Self-Priming: No buffer hopper needed.
- Easy Cleaning: Manual disassembly without tools.
Disadvantages
- Slow process: If high speed is required, two pumps are advised. It is slow to it non contiguous functioning (suction cycle, dosing cycle)
- Continuous flow: Large volume dosing renders pumps heavy and difficult to handle.
- Maintenance: For high level of sanitary application daily disabling and cleaning is required.
Flow sensor
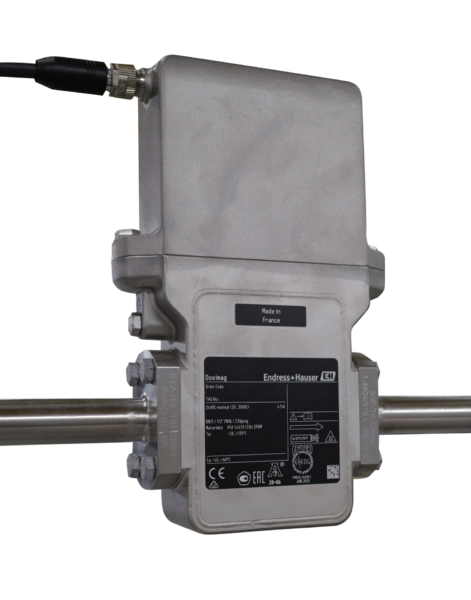
Provides critical data for process control and monitoring.
Key Features:
- Measurement: Tracks liquid dosing realtime.
- Types: Includes electromagnetic sensor.
- Real-Time Data: Provides immediate feedback for process adjustments.
- High Accuracy: Dosing accuracy below < 1%, ideal for handling differential product parameters like viscosity, varying product supply pressure, and varying temperature.
Applications
- Technical products: Accurate flow measurement and control.
- Food: Accurate flow measurement and control.
- Pharmaceutical: Accurate flow measurement and control.
Advantages
- Precision: Accurate dosing and flow measurement.
- Versatility: Handles various fluids and changing conditions.
- Real-Time Monitoring: Enables immediate process adjustments.
Disadvantages
- Installation Cost: Can be high, especially for precise models.
- Complexity: May need specialized knowledge for setup and maintenance.
Mass flow sensor
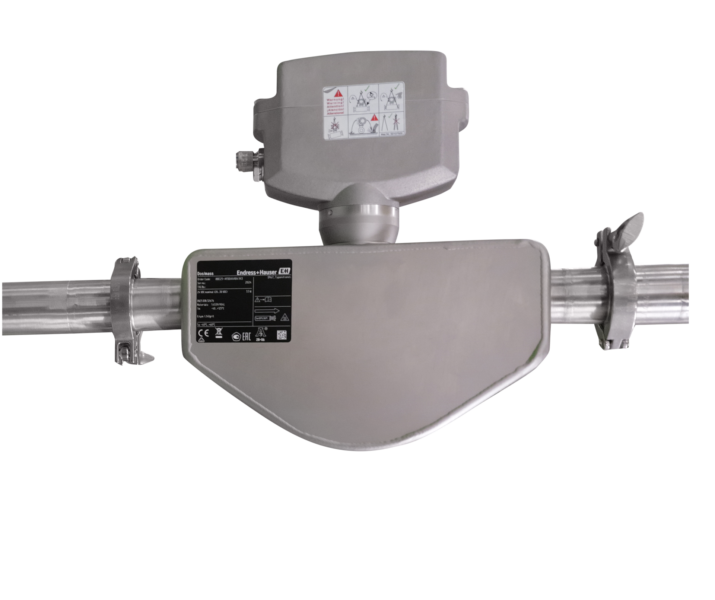
Measures the mass flow rate of fluids with high accuracy, regardless of changes in temperature, pressure, or viscosity.
Key Features:
- Mass Measurement: Directly measures mass flow rate of liquids even with certain gas concentration inside.
- Types: Includes Coriolis sensors.
- High Accuracy: Precise mass flow data, below <1%.
- Versatile Performance: Effective for almost all products, including those with gases or dissolved substances, such as beer or other foamy products.
Applications
- Industrial Processes: Accurate measurement in manufacturing and chemical processing.
- Food and Beverage: Ensures precise dosing and blending.
- Pharmaceuticals: Monitors fluid flow for consistency and compliance.
- Energy: Measures fuel flow and monitoring in combustion processes.
Advantages
- Precision: Accurate mass measurement, regardless of fluid properties.
- Real-Time Data: Immediate feedback for process control.
- Versatility: Handles a wide range of fluids, including those with gas or foam.
Disadvantages
- Cost: Higher initial investment compared to regular flow sensors.
- Complexity: More complex installation and maintenance.